Solar energy systems are an advanced and evolving technology that creates clean, renewable energy. Solar panels can lower your electric bill while reducing the use of harmful fossil fuels, making solar systems both financially and environmentally beneficial. The ability to harness solar power is a key factor in creating a green, sustainable future.
While solar panels continue to gain traction in residential and commercial usage, there are still many questions from current and potential users. Most people are aware of solar panels’ function as clean energy technology, but the details of solar panel construction and utilization can be hard to understand. Many wonder, how solar panels use only solar energy and still maintain such high efficiencies. This is a fair question, and the answer lies in the details of solar panel construction.
Solar panels are a high-tech, complex invention. Many different solar panel components make up the shining panels you see in real life and online. When discussing solar panel construction, we need to break it all the way down to the very fibers of the device. Let’s start at the beginning.
WHAT GOES INTO SOLAR PANEL CONSTRUCTION?
Understanding how solar panels are made is very useful. In knowing about solar panel construction, you can make more efficient and knowledgeable decisions in your path to solar energy. It’s essential to remember that solar systems should benefit you directly. The best way to make sure that happens is to understand solar panel construction and its applications.
Let’s tackle the first big question. How are solar panels made?
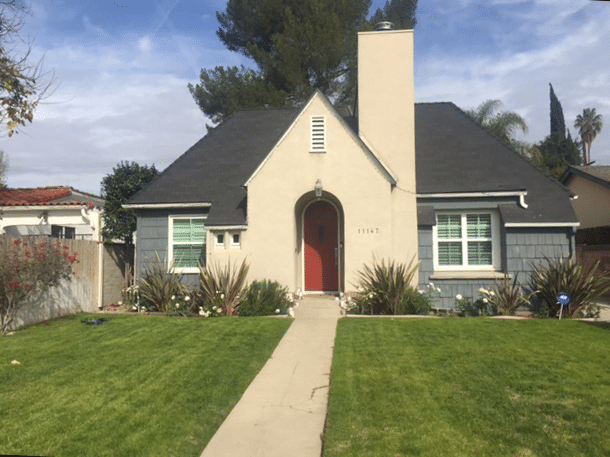
Solar panels are composed of solar photovoltaic (PV) cells that work by absorbing sunlight and converting it to solar energy. These PV cells are manufactured with crystalline silicon cells. These cells are very delicate and need to be handled with great care in the solar panel construction process. Crystalline cells used in solar panel construction can be one of two types: monocrystalline or polycrystalline.
Since these crystalline cells make up the base of solar panel construction, they are highly important in determining a solar system’s energy efficiency. The more efficient the crystalline cells, the more efficient the panel itself will be.
Monocrystalline vs. Polycrystalline Cells
Monocrystalline cells are known to be the most energy-efficient type. The process of making these cells involves actively growing crystals, but the monocrystalline cell’s high efficiency comes with a cost. This procedure to make monocrystalline is more expensive to enact, making monocrystalline solar cells more expensive as well.
Polycrystalline cells can be made using an easier, less expensive method. Polycrystalline cells are formed using step-by-step purification processes. This means that polycrystalline cells’ production costs less, but it comes at the price of their efficiency. Polycrystalline cells are less efficient than monocrystalline.
To summarize, monocrystalline cells have a high production cost and high efficiency. Polycrystalline cells have a low production cost and lower efficiency. You might be wondering, is there some way to meet in the middle? The answer is yes!
In solar panel construction, there is a subsection of monocrystalline cells called cast monocrystalline cells. Cast cells are made using a casting process that is similar to the polycrystalline purification processes. This process makes cast cells cheaper to produce, but cast cells are able to maintain a similar efficiency to their pure monocrystalline brothers. While their efficiency is not as high as pure monocrystalline, it is higher than polycrystalline.
We know that the details of solar panel construction can be overwhelming, so let’s review one more time.
Monocrystalline cells are created using a pure crystal growing procedure. They are the most expensive to produce and have the highest efficiency. Cast monocrystalline cells are created using a casting method that is cheaper than the pure crystal growing procedure. They are inexpensive to produce and have high efficiency. Polycrystalline cells are formed using a purification process. They are the most inexpensive to produce but have a lower efficiency.
Crystalline Silicon Cells
We’ve gone into great detail about crystalline silicon cells, but how exactly are they manufactured? It starts with sand.
Silicon is pulled from sand, called silica sand. The silica sand is then purified and processed to form a pure polycrystalline silicon cell. The polycrystalline silicon cell is melted and cast into large rectangular blocks. The blocks are thinly sliced to produce polycrystalline cells–the very same polycrystalline cells used in solar panel construction.
To produce the energy-efficient monocrystalline, additional steps are required. The polycrystalline silicon needs to be melted under high pressure and temperature to enact the crystal growing process. This will slowly grow a single monocrystalline crystal called an ingot. The ingot is then cut into thin wafers. The wafers become an integral part of further solar panel construction and efficiency.
MORE SOLAR PANEL COMPONENTS
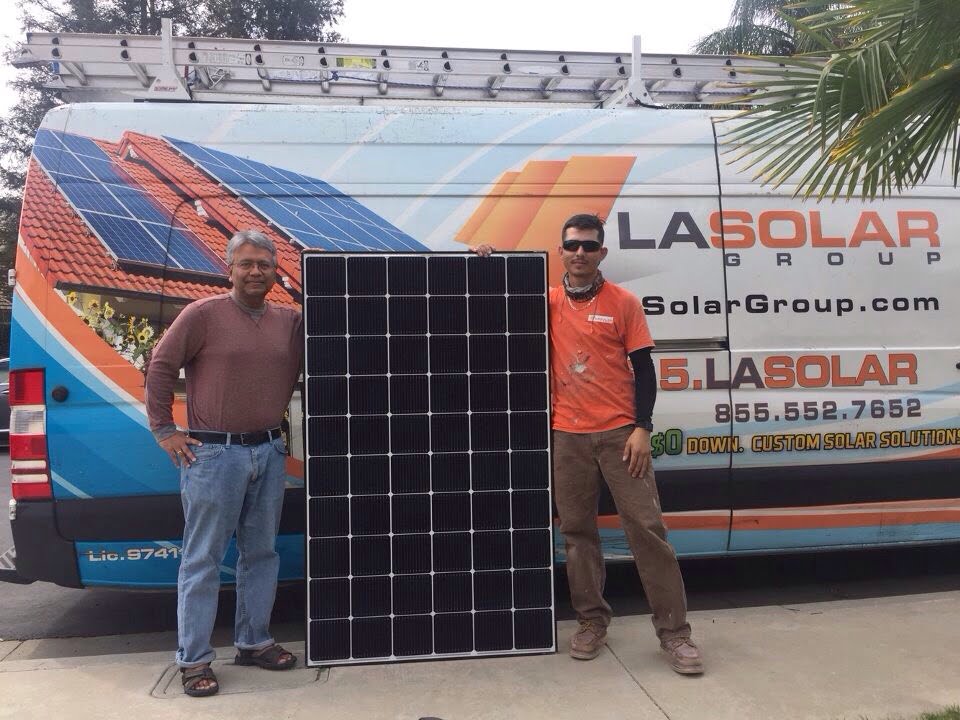
Now that we know how solar panels’ efficiency is determined, we can look a little deeper. After all, solar panels are not made up of only crystalline cells. There are six main components of silicon crystalline solar cells–the most popular and common form of solar panels.
While silicon crystalline solar cells are the most frequently used, there are other kinds of solar panels on the market. For example, there are thin film or screen printed cells in circulation. However, these cells have limited uses and are constantly being adapted and developed. Currently, when discussing solar panels, silicon crystalline solar cells are considered to be the norm.
Solar panels have several important components: solar PV cells, aluminum frame, EVA film, backsheet, glass, and the junction box and its connectors.
Solar PV Cells
Solar PV cells are one of the most important features in understanding the question: how are solar panels made? PV cells function by absorbing sunlight and converting that solar energy into DC electrical energy. As mentioned before, the efficiency of the PV cell depends on the crystalline used in production (poly or monocrystalline). Most residential solar panels consist of 60 interconnected mono or polycrystalline cells. Commercial solar panels are larger and therefore consist of more interconnected cells. Often, commercial solar panels are made of 72-96 mono or polycrystalline cells. Due to the increased cell count and size of the panels, commercial solar panels generate a higher voltage.
Aluminum Frame
Aluminum frames are another necessary solar panel component. These frames protect the portion of the panels that shelter the cells. The frame also provides a steady and solid structure on which to mount the solar panels. Depending on the solar panel construction and manufacturer, corner sections of the frame can be screwed, pressed, or clamped together.
The manner in which the frame is put together will provide different levels of strength and stiffness. The frames are made to withstand extreme external forces like high winds. Solar panel construction must focus on durability, as solar panels will often face the outdoor elements.
EVA Film
Ethylene-vinyl acetate (EVA) is a plastic polymer used to gather the cells and hold them together during production. As with most solar panel components, EV film needs to be highly durable to external forces. Having tough and resistant solar panel components increases your solar system’s lifespan and saves you money in the long run.
In solar panel construction, EV film is used for covering the sides of the solar panels. With this EVA protection, panels can better withstand shock and vibrations (think: hailstorms, heavy rain). High-quality EVA films can make or break solar panels’ long-term survival. With a low-quality EVA film, water entry can happen and this will greatly reduce the panels’ efficient lifetime. During solar panel construction, solar cells are covered with EVA film before being gathered within the glass and backsheet.
Backsheet
The backsheet acts as a moisture barrier and a mechanically protective, electrically insulated solar panel component. In solar panel construction, the backsheet is placed in the rear. Backsheets are typically designed with plastic polymers.
They have different levels of UV resistance and long-term protection, depending on the type of backsheet that is used. It is typical for the backsheet to be white in color, but there are also clear or black options available. The color depends on the manufacturer and module of the system.
Glass
A glass sheet is another necessary solar panel component. It is placed on the front of the solar PV cells for protection in case of weather-related issues. The glass is thick, usually 3.0 to 4.0 mm. It is tempered and designed to withstand extreme weather conditions and heavy mechanical loads.
Manufacturers commonly use high transmissive glass because it improves light transmission and, thus, solar energy consumption. Ensuring high solar consumption is a key design element in solar panel construction.
Junction Box and Its Connectors
The central point of all solar panel components is the junction box. This is the place where all the sets of cells are connected to one another. The junction box can be found on the rear side of the panels. Since the junction box is the point of connection for important pieces like the cells, it needs to be weather-proof and protected from any possible dirt or moisture. A durable junction box is a necessity in solar panel construction.
The junction box holds bypass diodes, which are used to reduce the loss of power solar panels experience when shaded or dirty. Diodes can lose their efficiency over time, so they may need to be replaced. For this reason, the cover of the junction box can be removable for servicing. In newer and more modern panels, there exist long-lasting and advanced bypass diodes. In this case, the junction box may not be designed to open as there is no serviceable need.
Another connector housed in the junction box is solar MC4 connectors. These connectors are weather-resistant, secure, and UV resistant. Junction boxes are very important in solar panel construction, as they link all sets of cells together.
WHAT IS THE PROCESS TO MANUFACTURE SOLAR PANELS?
Solar panel construction and manufacturing take place in advanced facilities with robotic equipment. These high-tech pieces of equipment and sensors are used to maintain precision accuracy. Facilities must be kept to high cleanliness standards to ensure that no contamination results during solar panel construction.
In the manufacturing process, solar panel components are treated with great care and evaluated with optical sensors to ensure the panels are in perfect working condition. The crystalline cells are very fragile and must not be cracked or broken in the assembly process.
A number of tests are performed following the competition of solar panel construction, for example, flash testing. These tests and checks are meant to evaluate the panels for any damages or defects. As solar panels are going to be exposed to sunlight and high temperatures for many years, it is imperative that they leave the manufacturing facilities in mint condition.
MOVING FORWARD IN YOUR SOLAR JOURNEY
There is a lot to understand regarding solar panel construction and implementation. With all the information that is out there, it can feel intimidating to research the complexities of solar panel components. At LA Solar, we are here to assist you in your learning process. It is our priority to make the information available and as easy to follow as possible.
Different solar panel companies will offer their own unique range of products and services, and it can be hard to choose what is right for you. The more you know about solar panel components, the better off you will be. Understanding solar panel construction is the first step in making the right solar decisions. Now that you know about all of the different solar panel components and forms of solar panel construction, you can safely move forward with your solar journey–all while ensuring you get the best results possible!